Route 132 rebuild - by the numbers
"A good rule of thumb is that every mile of road costs at least one million dollars to repave." – Roadbotics.com
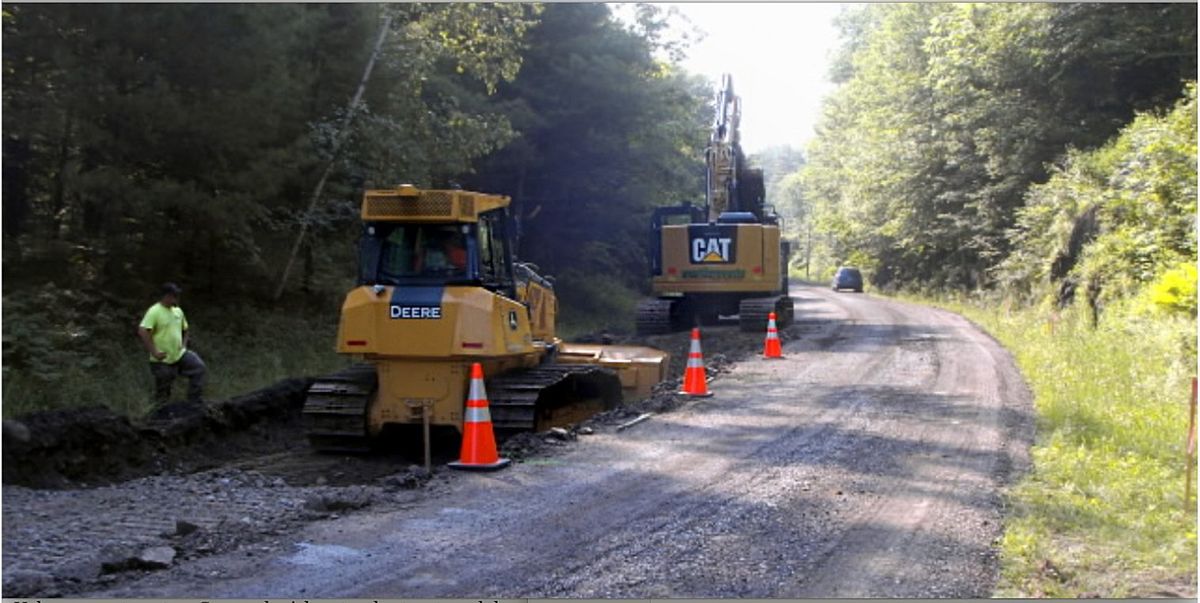
At a contracted price of $3,485,175, the rebuilding of the approximately three and one-third miles of Route 132 between Tucker Hill Road and the Norwich town line stands to cost the town about one million dollars per mile. Although this sounds staggering, it is actually pretty much the norm. According to sources such as Roadbotics.com, “a good rule of thumb is that every mile of road costs at least one million dollars to repave, taking into account labor, equipment and paving costs.”
All the details of labor and equipment may be gleaned from the weekly and biweekly reports from Seth Potter, the Resident Inspector of this phase of the Route 132 rebuilding, who was on-site daily in his role of performing quality control and supervision. Seth is employed by Stantec Engineering, the designer of the road rebuild.
Labor included a survey crew to lay out the project according to Stantec’s design. The crew consisted of two transit operators assisted by two survey technicians. Then came the personnel from Northwoods Excavating Inc., the company that won the bid for the project. Their workforce was eight truck drivers, four heavy equipment operators, between one and four flaggers, one layout supervisor, and one project superintendent.
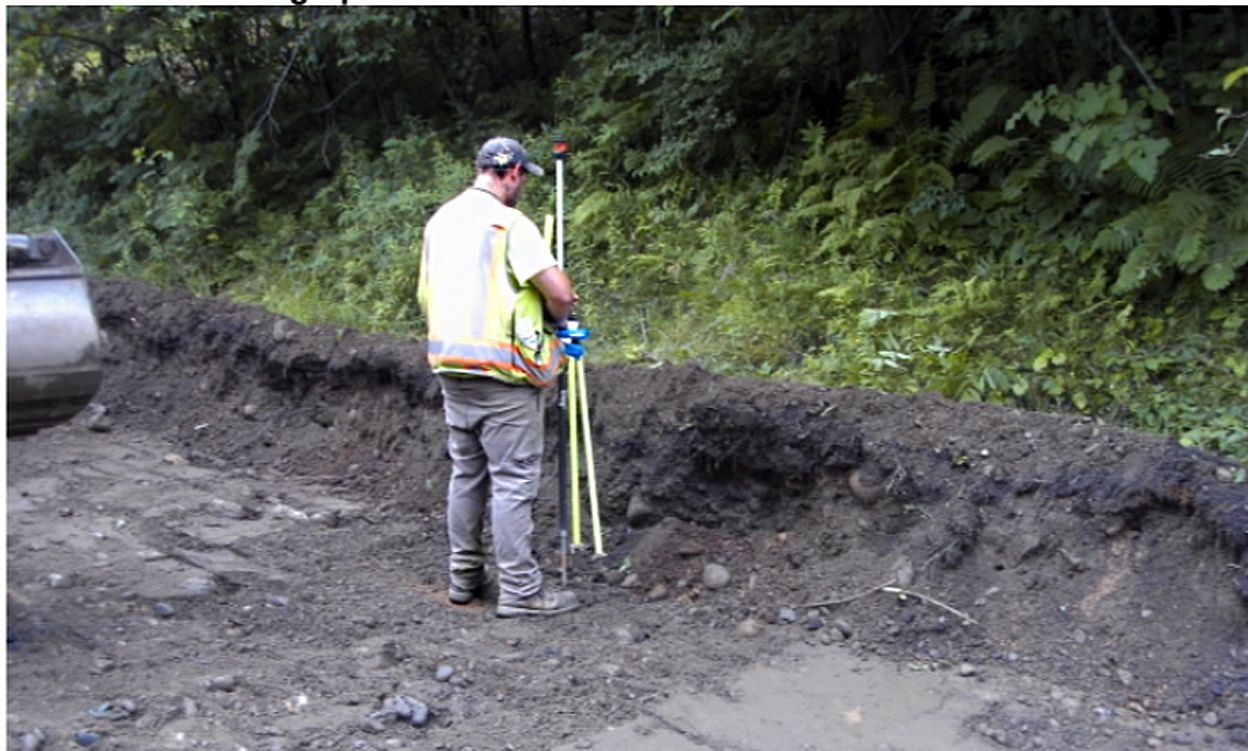
Northwood’s workers operated the following array of equipment: six ten-wheeler dump trucks, two Volvo excavators, two crew-cab pickup trucks, two trench boxes, two Jumping Jack compactors, one 400 pound compactor, one loader, one water truck, and an assortment of “miscellaneous tools.”
The six dump trucks were needed for multiple uses: to carry away the torn-up asphalt of the old road and later return it as reclaimed material for rebuilding; to truck away and dispose of the excavated road layers below the asphalt; to bring in gravel for the new road bed plus various types of fill for ditches and drainage; and to move heavy or large objects like culvert headwalls and culverts. Excavators are capable of rotating their cab with digging arm through 360 degrees and of lifting huge loads of soil or debris. They dug out the old road material and carefully shaped the “road box,” a wide, flat-bottomed trench 20 inches deep, that defined the structure of the new road. The road box followed the survey lines designed by Stantec and will be an improvement over the old road geometry. The loader is a versatile and powerful machine that is likened to a giant shovel. Its job was to move piles of materials around the work site or load them into trucks.
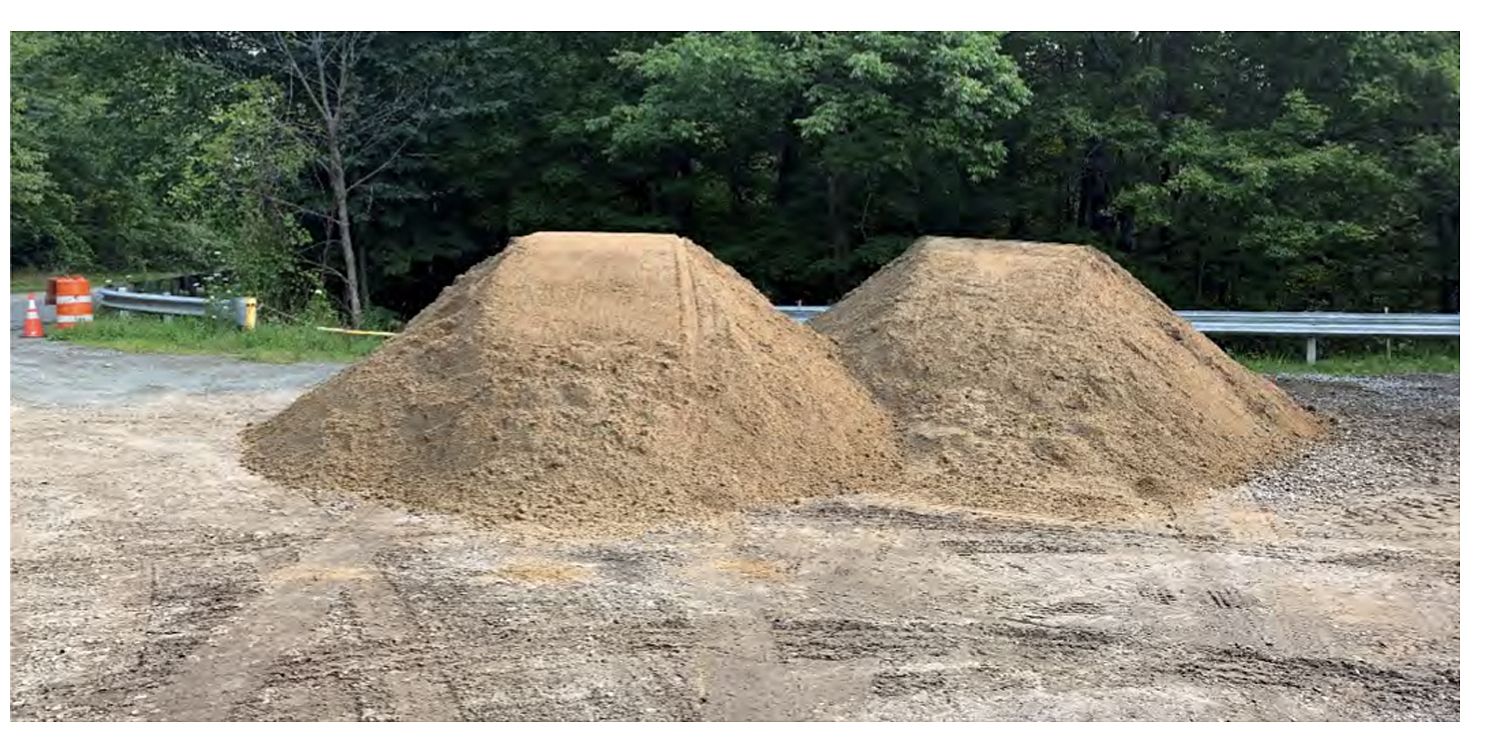
Trench boxes are vital pieces of safety equipment. Their function is to keep the sides of a trench from collapsing inward on workers. Finally, the water truck wets down surfaces and is necessary to control dust.
In spite of this lineup of machinery, Northwoods does not have specialized equipment or trained workers to cover every aspect of rebuilding and repaving a road. Like all contractors they delegate some work to subcontractors.
Garrity Asphalt Reclaiming Inc., based in CT, was hired for the job of road reclamation, a process in which the old road pavement is ground up so it can be dug up and reused. Their labor force was one laborer and one foreman who also operated the specialized reclaiming machine. For this job they only needed one reclaiming machine and one crew-cab pickup truck. The reclaiming machine grinds up and pulverizes the asphalt surface into a form that is reusable. In essence, it’s a large rotating drum equipped with rows of carbide-tipped teeth that grind away the asphalt. It will not pulverize rocks, however.
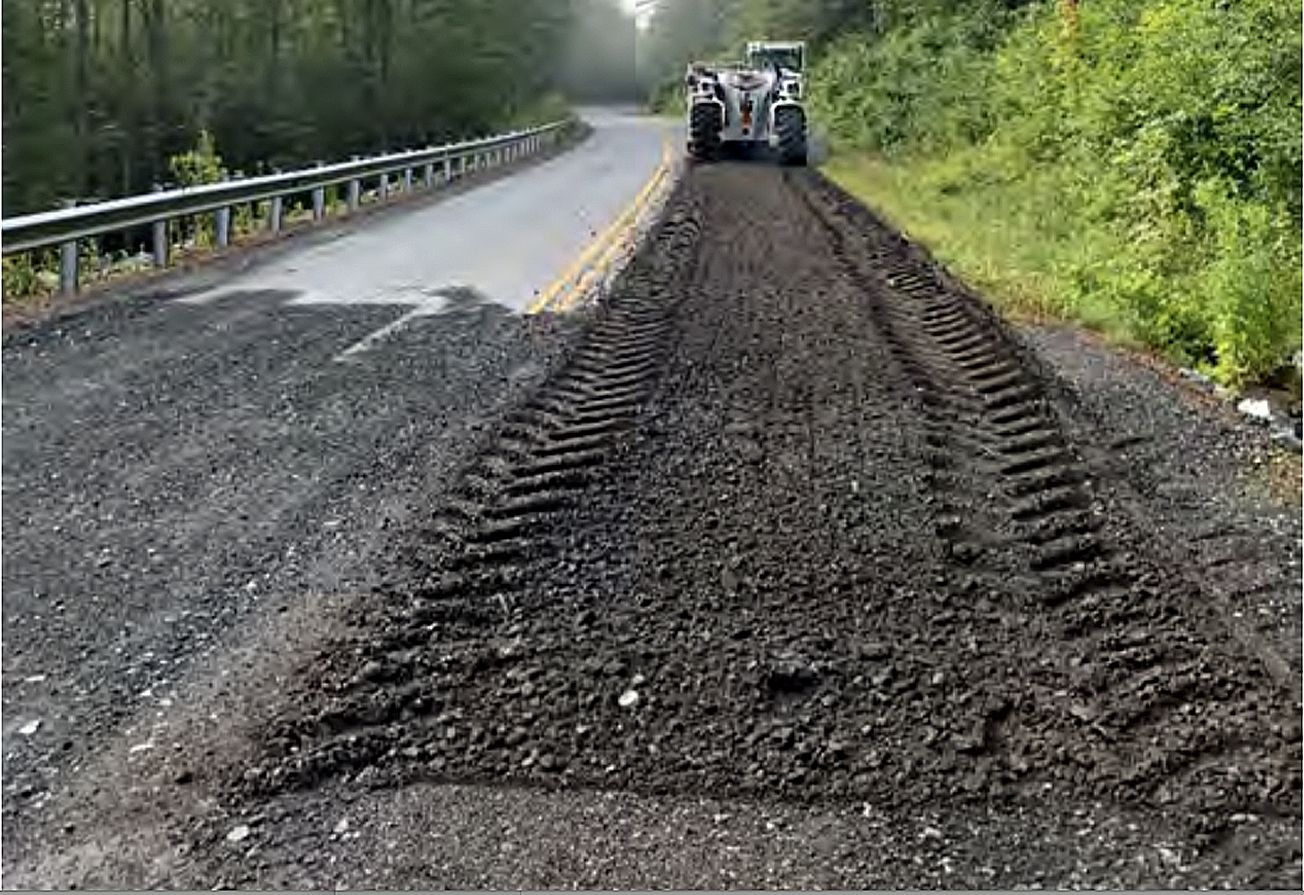
The second subcontractor was Lafayette Highway Specialties from Essex Junction, VT, a company that installs guard rails. Their workers were three laborers, and one foreman who doubled as equipment operator. Their equipment consisted of the following: one transport truck and one crew-cab pickup truck.
The third subcontractor was J. Hutchins Inc., a company that specializes in asphalt. They have a state-of-the-art asphalt and aggregate plant in Irasburg, VT. They came with a crew of five operators and one foreman. They were equipped with two 8-ton vibratory rollers and one CAT Paver (hot asphalt paving machine).
Last but not least, one representative from S.W Cole, a company that specializes in geotechnical engineering and testing of construction materials, including field testing, was on site to perform compaction testing on the installed road base gravel.
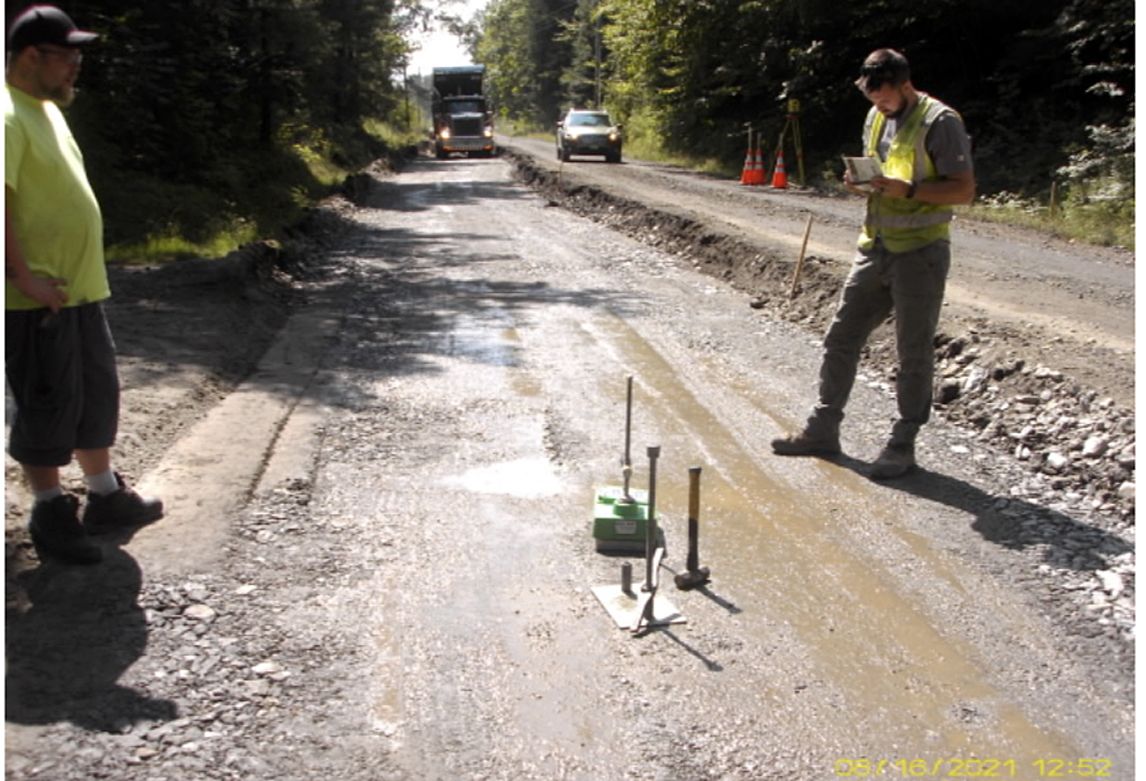
The start date, according to Seth Potter’s reports, was June 7th. By June 14th Garrity Asphalt’s big machine had ground up the road surface from the Gove Hill intersection to a little south of Cream Street. Northwoods workers had split into two crews, one excavating the reclaimed asphalt and then removing the underlying earth to a depth of 20 inches to "box out" the road. Gravel for the road sub-base (the layer below the asphalt) was laid in the trench, compacted, and the degree of compaction verified to meet the industry standard of 95% or more of dry weight density by S.W. Cole. Though far more time-consuming than asphalt reclamation, the boxing-out and sub-base made good progress at 250-300 ft a day of full road width. The projected speed had been 250 ft/day. The second crew took on the replacement of 14 road culverts and 8 driveway culverts, a task that would continue through fall. This work entailed excavating and removing old culverts, digging the culvert bed at the correct angle and slope, installing the new culvert in a bed of well-draining material, then filling to the appropriate grade. Meanwhile Lafayette installed 1,400 feet of “guard rail for construction” in lieu of using concrete safety barriers (Jersey barriers) for the project.
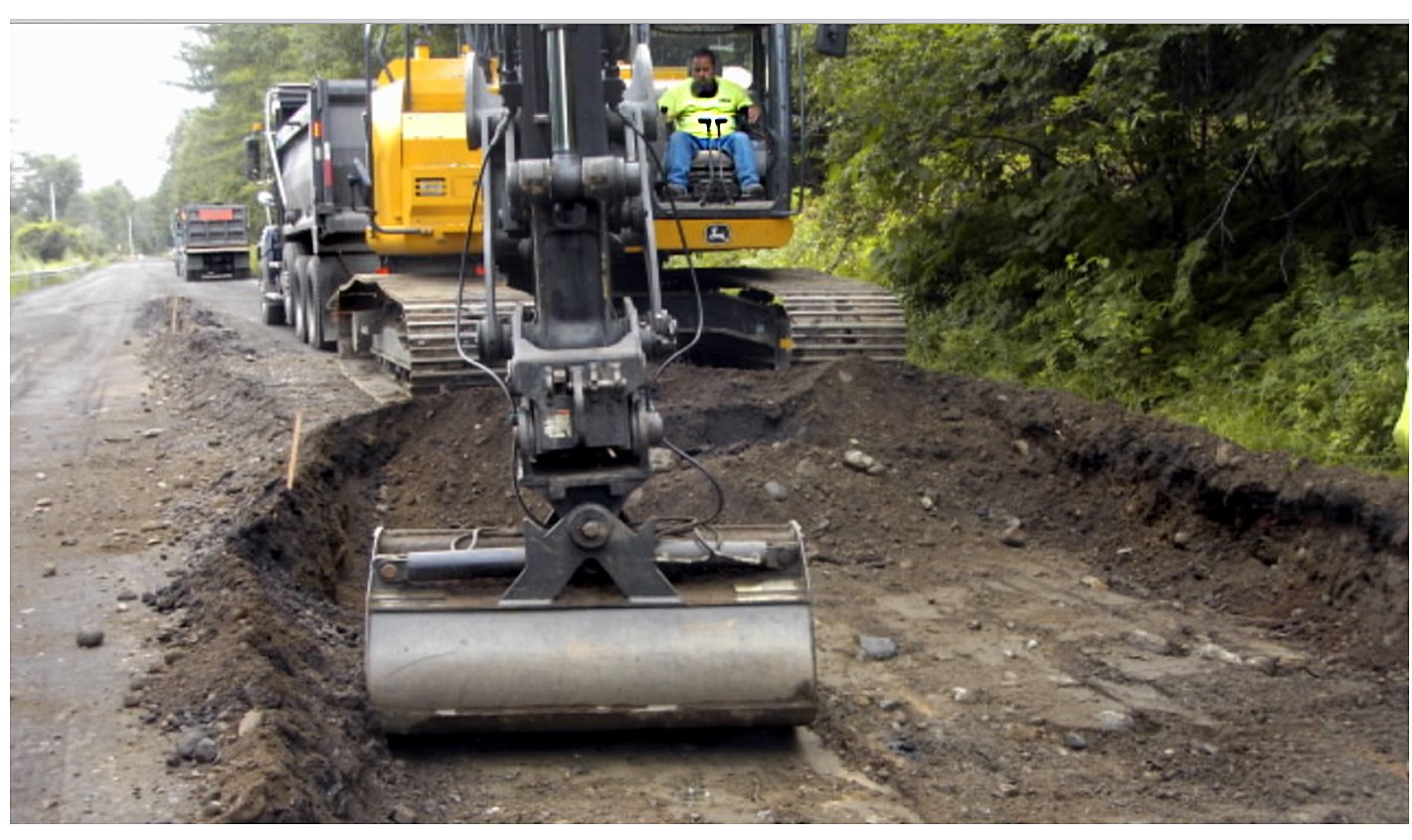
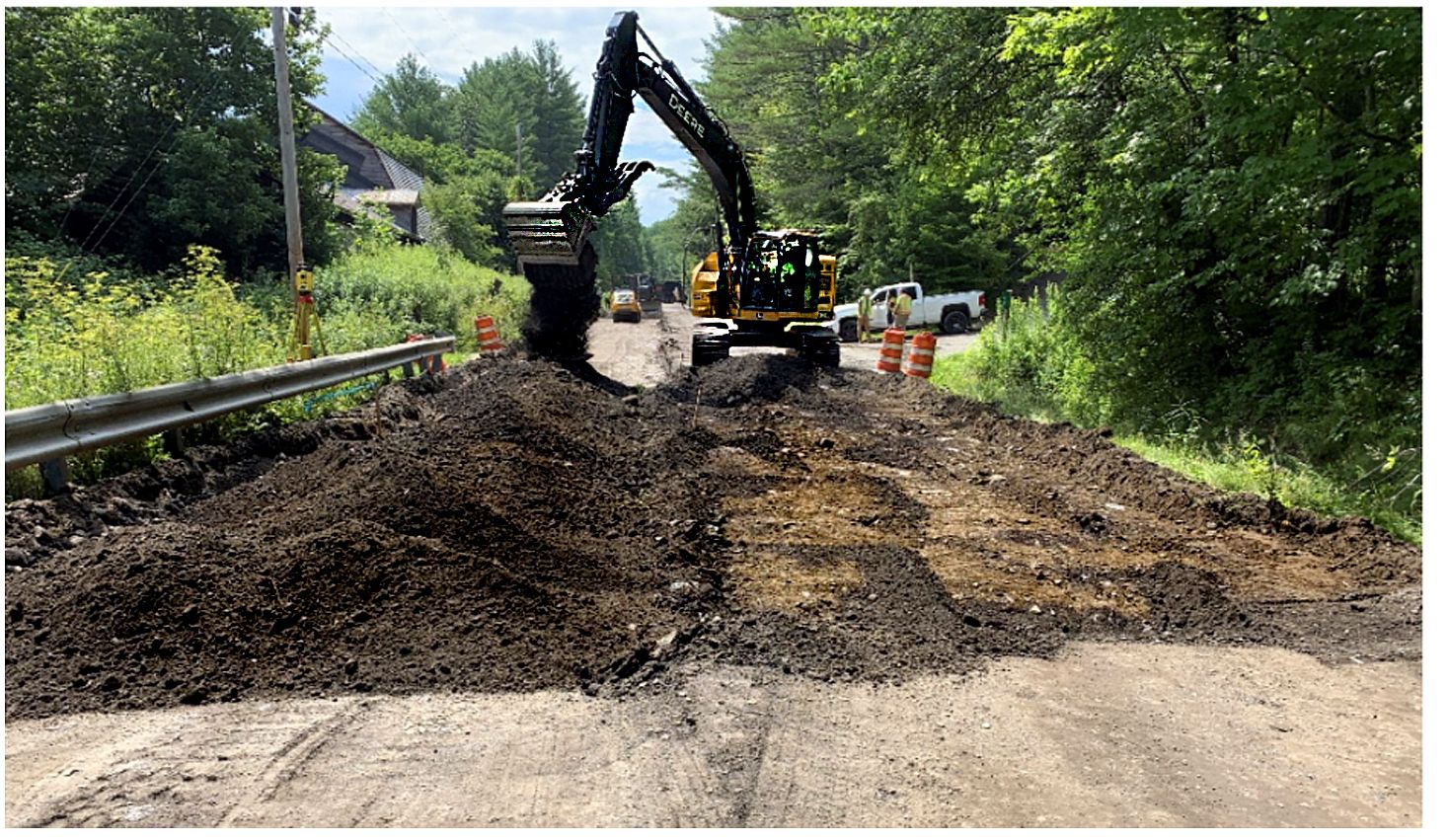
By July 23 the box-out and sub-base had nearly reached Cream Street. Remaining large (36-inch) culverts had been replaced. Garrity returned to the project site and completed the asphalt grinding at an average of 2,400 ft/day for the full road width, by July 30th.
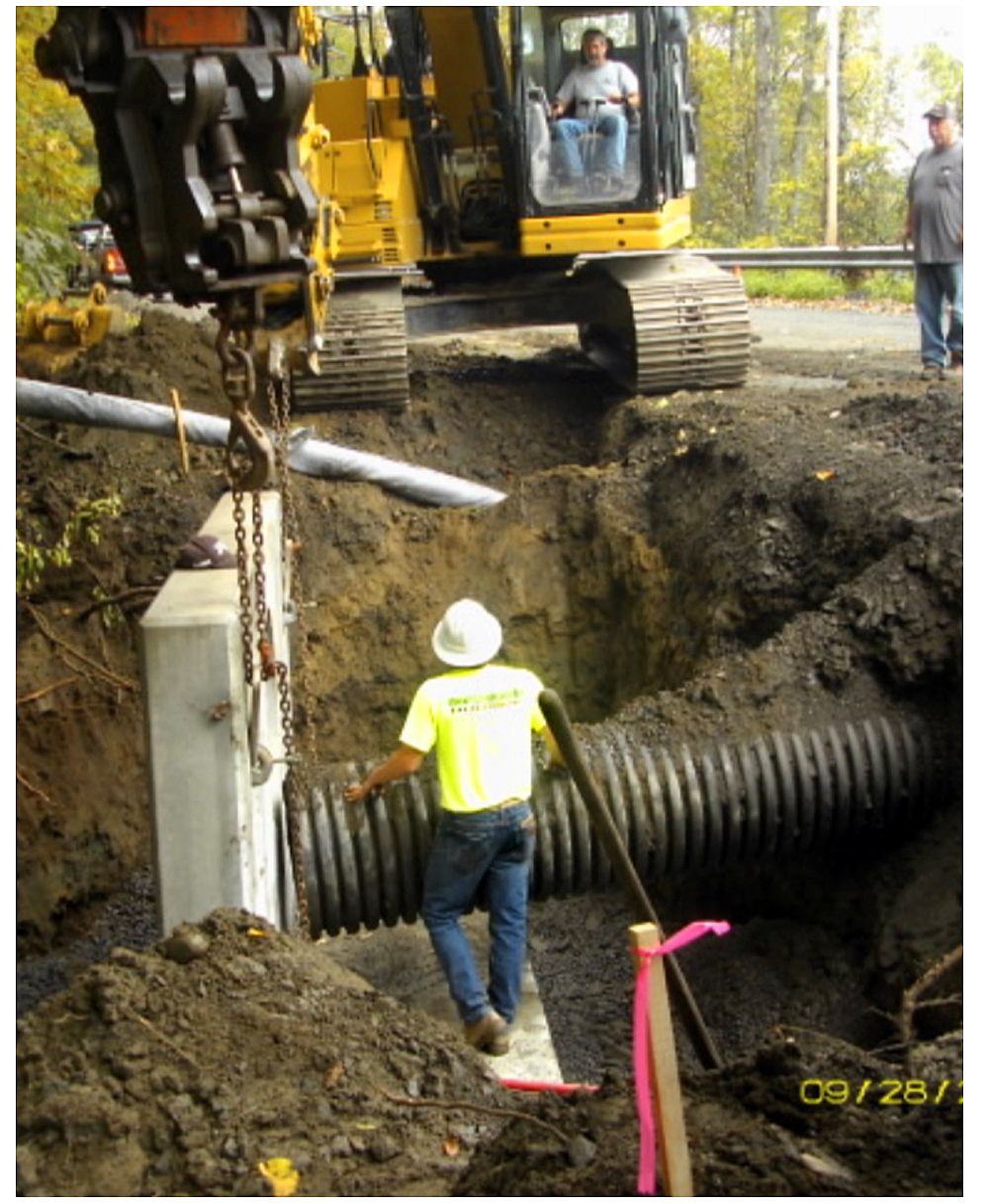
By August 20th the box-out and sub-base were still progressing. Meanwhile, a large culvert near Gove Hill required installation of a headwall. By September 10th the box-out and sub base were complete, and Northwoods crews were preparing the new culverts for addition of “flowable fill” material (which superficially resembles concrete, but is not concrete). They also added rip-rap aprons in drainage areas and culvert headwalls.
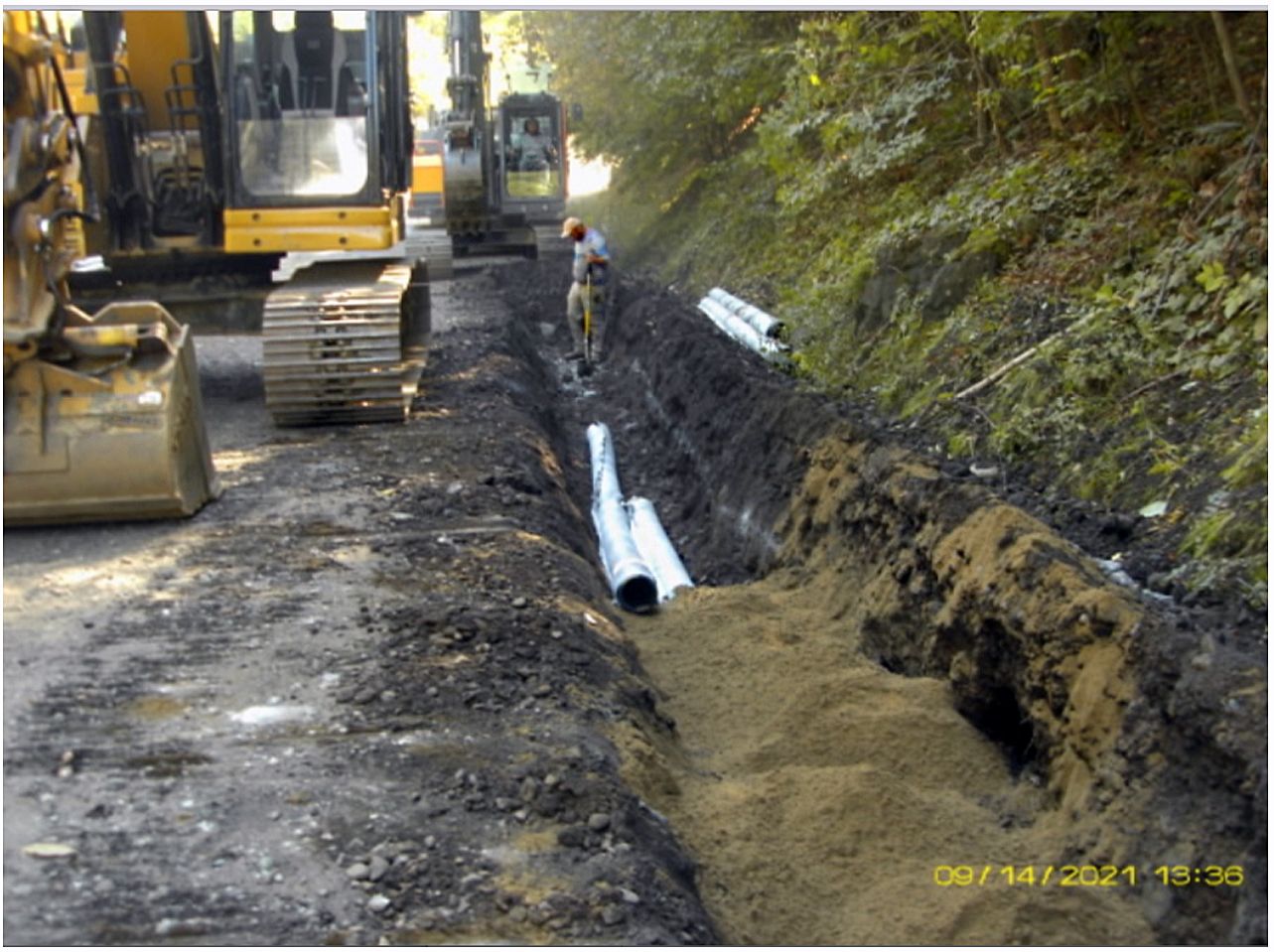
Other fall season work included the time-consuming installation of road underdrains along the length of the project. Northwoods provided some additional equipment: three trailers for transporting the long pipes. The purpose of this subterranean underdrain pipe system is to move water out of the road sub-base. Restricting the amount of water in the sub-base maintains the strength of this layer and generally helps the longevity of the road. By mid October 75% of the underdrains were installed. Other ongoing tasks were digging ditches, adding gravel to road shoulders, and grading them.
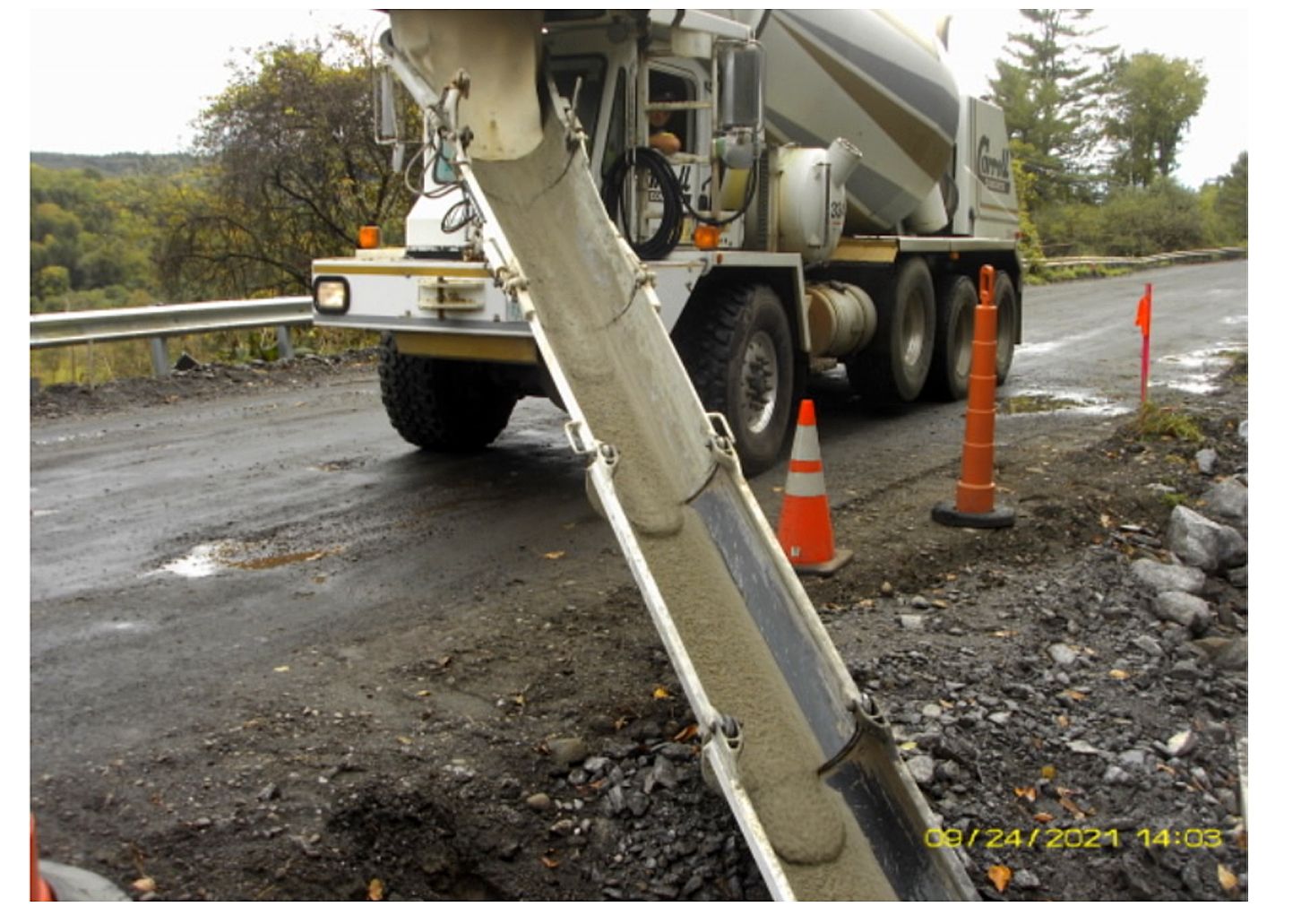
In late October Northwoods graded and loosened up the surface gravel/reclaim material and placed so-called “shim gravel” on the roadway in preparation for the first layer of asphalt paving. Heavy rain on November 11th and 12th delayed work and caused Stantec to order more ditching at “warranted locations” of the project site. The road gravel/reclaim layer passed compaction testing, clearing the way for J. Hutchins Company to move in with their asphalt-laying equipment. The CAT (Caterpillar) Paver laid down about 4 inches of hot mix asphalt, the roadway “base course.” Wherever stretches of asphalt were joined, such as along the road centerline, the joins were saw-cut and a so-called “tack coat” of emulsified asphalt was applied to fuse the joints. The freshly laid asphalt was then rolled with an 8-ton vibratory roller. Meanwhile, one Northwoods team was digging ditches while a second crew was seeding ditches and installing erosion control fabric. They also removed old guardrails and graded the material beneath.
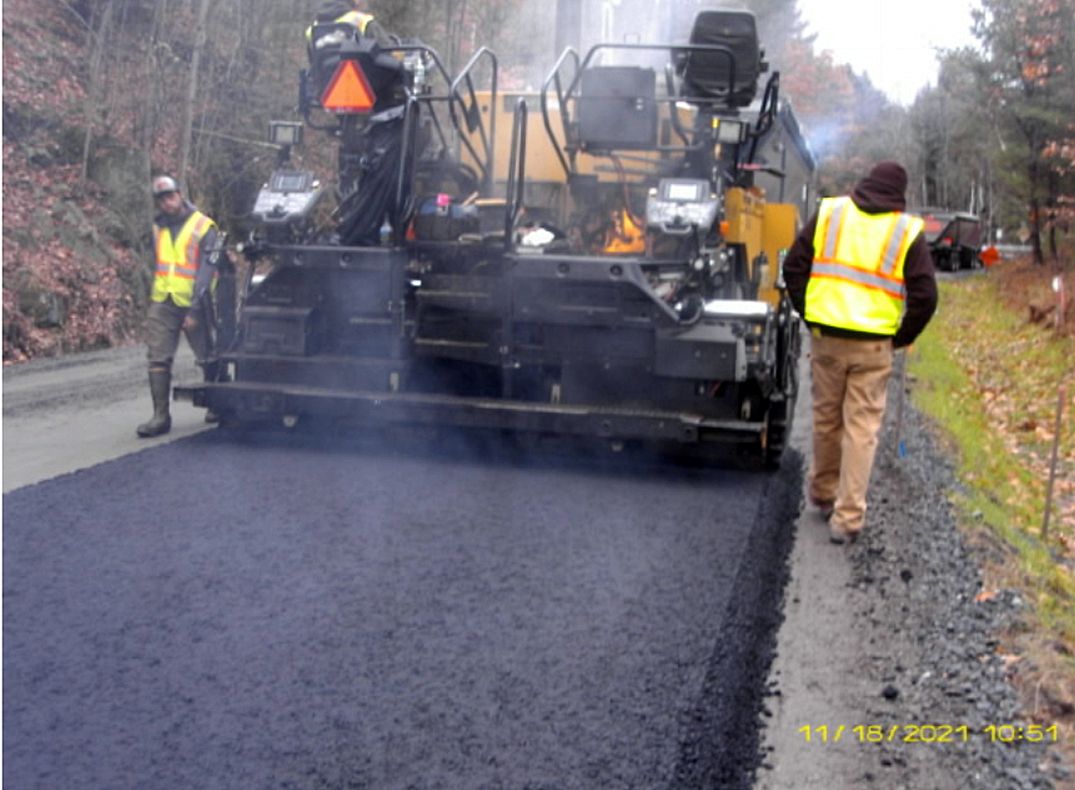
Finally Lafayette moved in again to install the permanent guardrails. Northwoods workers added gravel to the road shoulder to make a smooth transition with the new base course paving.
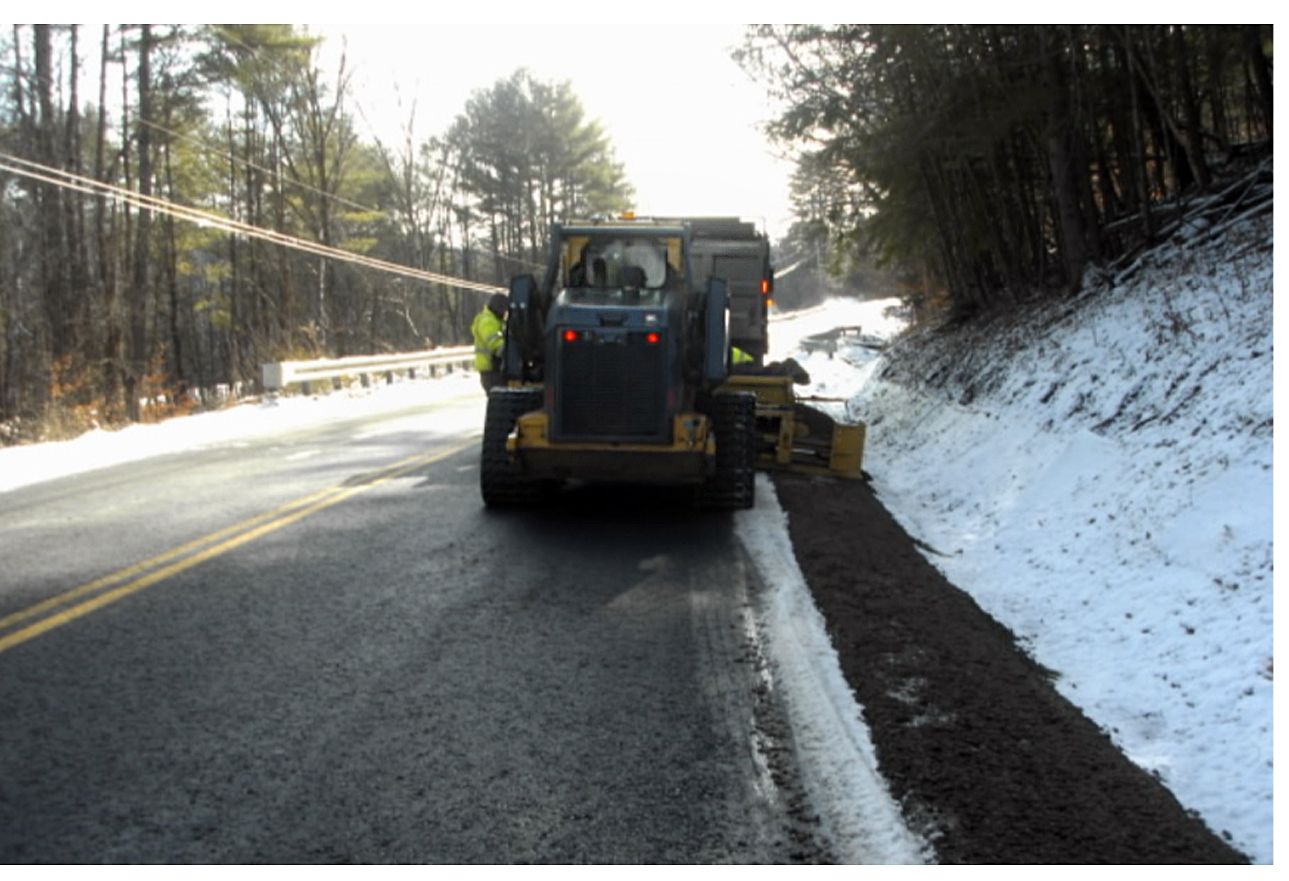
The survey crew completed their survey of the drainage installations to create a record of the system “as built” that would act as a reference for future road workers. The project finally closed down for the winter on December 17th. In the spring, we look forward to two inches of asphalt top coat.
Photo Credit: Stantec Engineering