Make hay - square or round - while the sun shines
As long as there are small fields to mow, horses to feed, and people like Ellis to run the equipment, the square bale will likely persist.
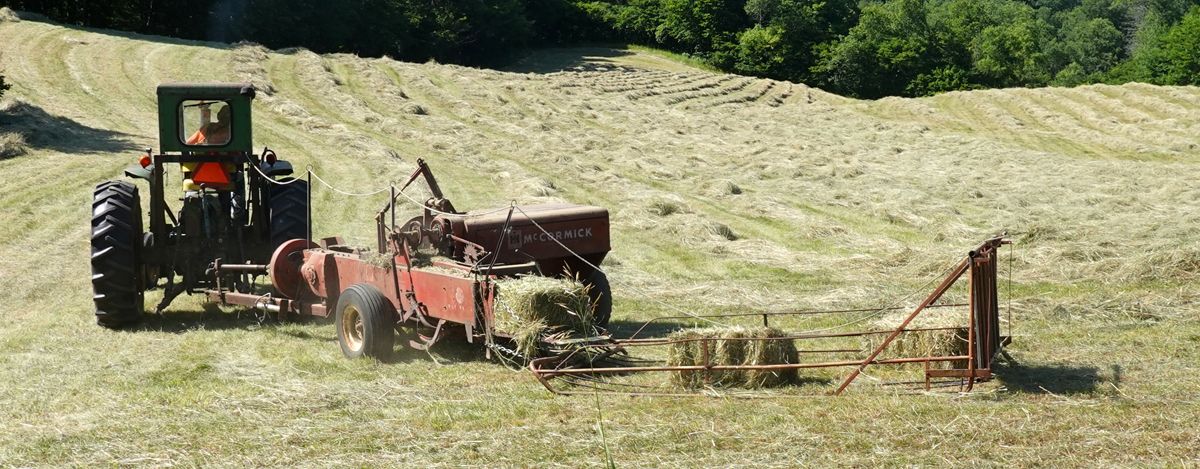
Vintage tractors are a familiar sight on Tucker Hill Road in the summer months. They belong to Ellis Paige, who boasts a collection of 13, mostly in working order. And the ones that can work, do, bringing in the hay harvest on a picture-perfect – albeit sweltering – day.
It’s a good thing that Ellis is a master at maintaining machines, because the traditional haying method uses several. First the hay must be cut by the mower that trundles behind Ellis’s 1974 Oliver tractor. The tractor runs the mower and other machinery via its PTO (power take-off shaft). In this case, it’s powering a disc mower (aka discbine tow-behind) named for its high-speed rotating discs with blades, aligned on a cutter bar that rides along the ground. The advantage of disc mowers is that they can cut any hay, no matter how thick or matted.
The hay is left on the ground to dry, but if it takes too long to dry, part of its nutrient value is lost. The tedder is used to speed up drying by spreading hay and fluffing it with spinning tines. It is run by another one of Ellis’s tractors, an Allis Chalmers from the 1970s. A second pass with the tedder is needed when the hay isn’t drying fast enough .
The dry hay is prepared for baling by moving it into windrows with yet another machine, the side delivery rake. Unlike his other haying machines, Ellis’s raker is ground-driven and doesn’t use a PTO. That means he can use the small blue tractor from the 1960s that works just fine, except the PTO is shot. The rotating teeth of the rake deposit the hay sideways into a neat windrow. Ellis has noticed that this also flips the hay over, exposing any damp hay underneath to the sun. In tough drying conditions he’s had to alternately use the tedder and side delivery rake several times to move drying along.
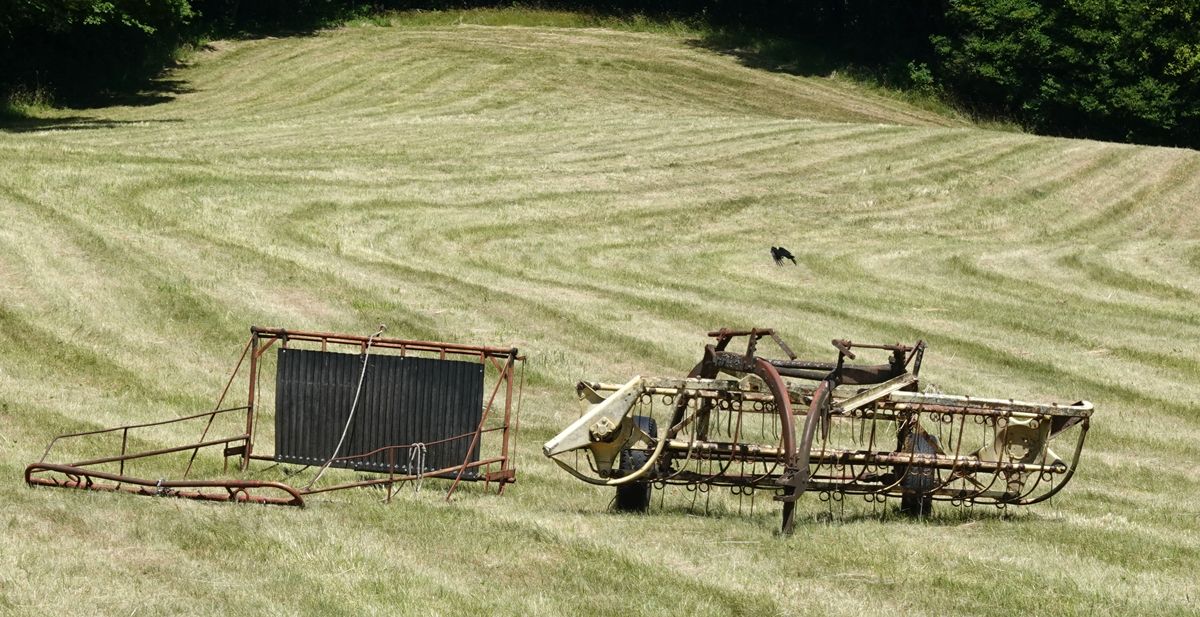
Only then does the baler appear, pulled behind, but to the right of, the Oliver. In this configuration, the baler passes along the windrow while the tractor travels between them. Several tasks go into the making of a square hay bale, and thus the baler is a clever machine. First the hay is raked up gently, to avoid picking up rocks and other debris. The hay is collected and fed in packets into the bale chamber by an auger. In the bale chamber, a plunger compresses the hay into a flattened square and trims the edges. The flat squares are aligned and held tightly under tension until there is a bale’s worth. Then two lengths of twine are wrapped around the bale by a movement of curved needles, and the twine is tied and cut by a geared knotting mechanism. The tying step happens in a matter of seconds and must be timed to avoid interfering with the other moving parts of the baler.
The completed bales are pushed out through a chute. In Ellis’s system, they fall into a sled-like hay rack towed behind the baler. As the tractor approaches the edge of the field near the road, Ellis pulls a cord to open the tailgate of the hayrack, depositing the bales where they can be picked up most conveniently.
The bales must still be moved to a dry storage area, typically in the hayloft above a barn. First they are piled into a truck, which sounds easy enough, except that a hay bale, even the so-called “small square bales” made by Ellis, weigh at least 50 pounds each. From the truck, the bales are transferred into the hayloft. Ellis recalls that he used to throw one bale with each hand, up into the loft, and could do it accurately, so the first bales landed at the back, the next ones progressively filling the middle, and the last ones at the front, saving the work of stacking them.
After all that comes the work of selling the hay. The economics of hay is a topic unto itself. Ellis figures it takes about three hours to mow 8-10 acres of hay, three hours each time it is tedded, three hours to shape the windrows, and three hours to bale it. Each three hours running a small tractor uses very roughly eight gallons of diesel, and for that he ends up with about 300 bales of hay. There are several pieces of equipment to keep in working order – six in all, counting the second and third tractor – and Ellis’s labor must be worth something, too.
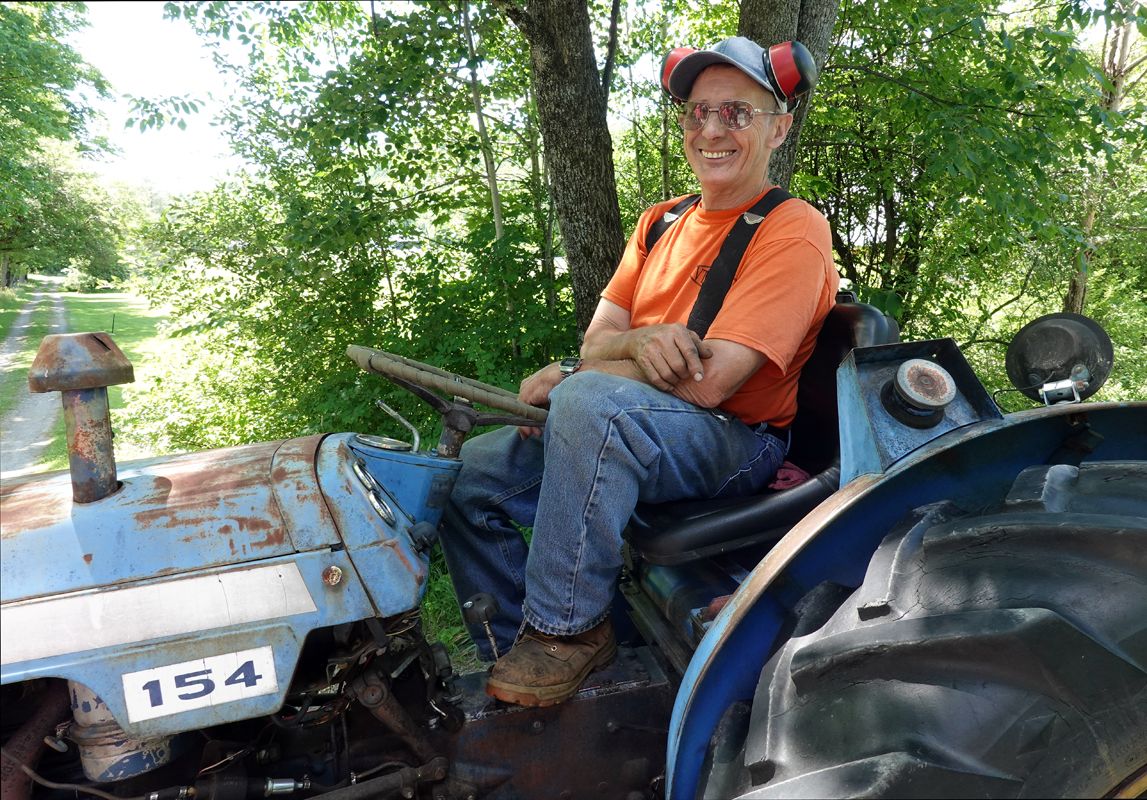
In spite of it all, his price per bale is very competitive. And, although it’s hard to believe, he is “retired” and, in fact, gave up his list of regular customers. Right now, family and neighbors, his usual takers, have hay left from last year’s bumper crop and won’t buy as much this season. He’s looking for places to store bales and people to buy them.
These days, small square bales are mostly sought for horses or small-scale livestock operations. They are reliably dry, making them better for the digestive systems of horses that don’t tolerate moldy hay the way cows can. They can be stored in modest spaces and, when properly protected, they retain their nutrient value better than the large round bales wrapped in netting that are touted as suitable for outdoor storage. The idea is that the tightly packed, rounded shape sheds rain, but outdoors they do absorb water and lose around 10% of their nutrients. This is avoided with the large, plastic-wrapped hay “marshmallows” that protect hay from the elements. The “marshmallows” come in two flavors – dry hay and so called “haylage.” This consists of hay packaged while still moist, so it ferments anaerobically within the plastic like silage in a silo, retaining more nutrients and protein than dry hay. Since large round bales weigh upwards of 1000 pounds, they are most suited to large-scale feeding operations and need the right equipment.
Small square bales are labor intensive and more expensive to produce than efficiency-oriented large round bales. But as long as there are small fields to mow, horses to feed, and people like Ellis to run the equipment, the square bale will likely persist.
Photo credit: Li Shen