From logs to lumber (in pictures)
Ellis Paige operates a private sawmill and transforms trees he harvests from his own land into valuable lumber.
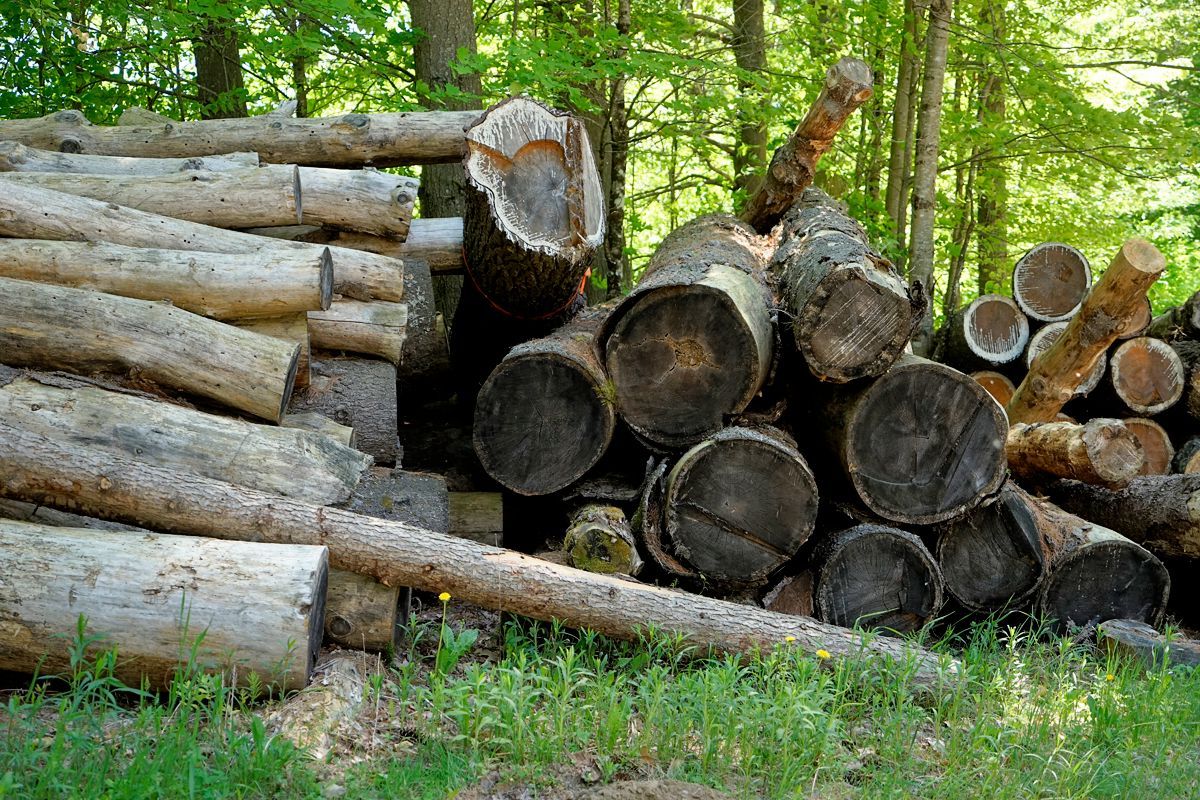
Most of us buy lumber from hardware stores and building suppliers and give little thought to the origin of the wood – where it grew or where it was milled. Even though timber from Vermont and New Hampshire forests was a foundation of the regional economy – and remains an essential commodity today – many small and midsized sawmills in the northeast folded in the late 1990s following the recession. Wood from our region is increasingly trucked to industrial-scale sawmills as far away as Canada. Meanwhile quality hardwood logs from the northeast are exported directly to China for that country’s burgeoning furniture industry. And, with the recent building boom in the U.S. coupled with shortages of home-grown timber, we’ve ironically begun importing softwood.
But there are some who buck the growing tide of globalization and our disconnected relationship with wood, a material that is essential to our daily existence. While small independent sawmills have largely disappeared, there remains one, right under our noses, in Thetford Center. About a mile from where a water-powered mill once ran on the Ompompanoosuc River, Ellis Paige operates his private sawmill and transforms trees he harvests from his own land into valuable lumber.
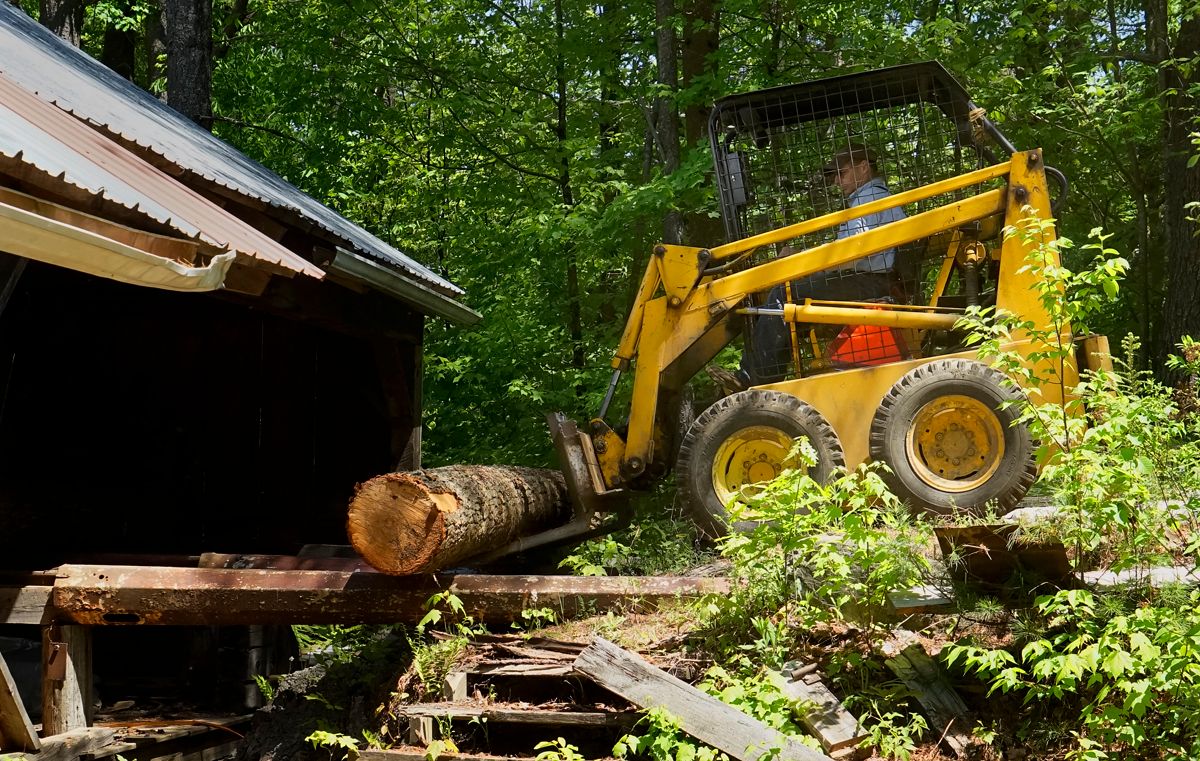
Ellis owns and operates an impressive array of equipment. He uses a small forklift to move logs one by one to the working entrance of the sawmill. The opening is just large enough to squeeze in an 18-foot log.
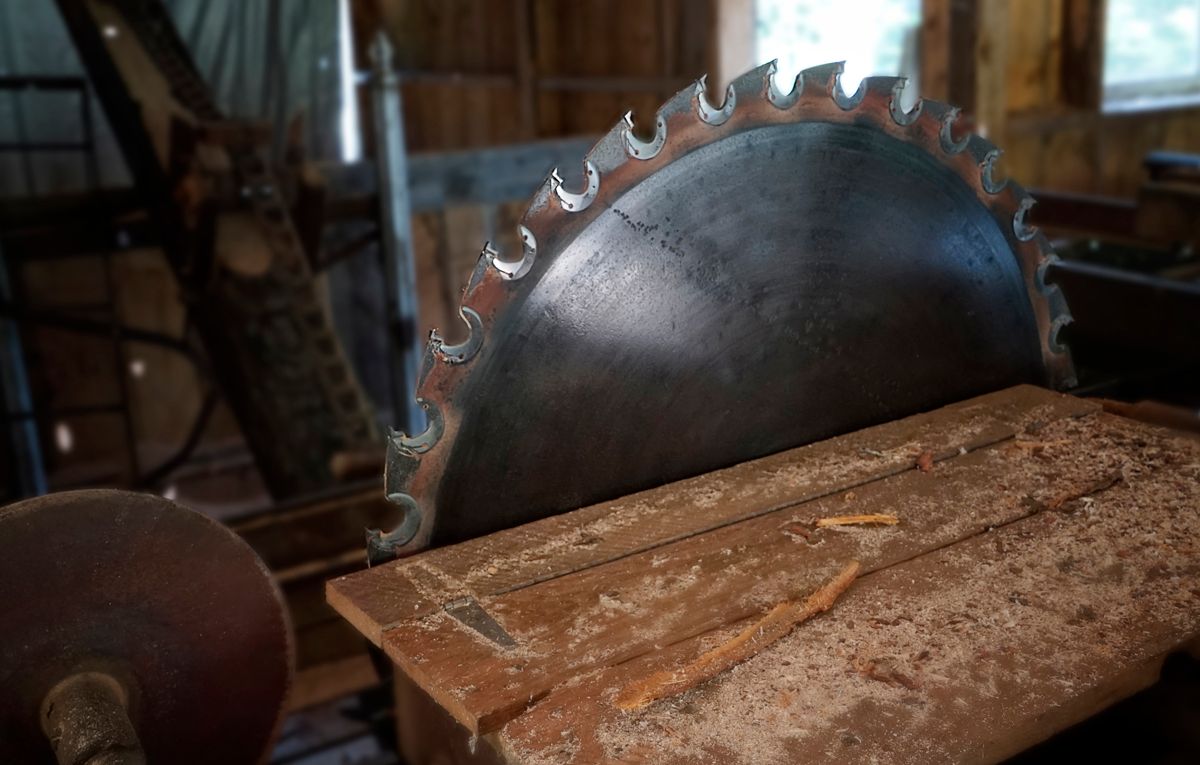
The business end of the operation. The sawblade can cut logs up to 17 inches in diameter. Larger logs, up to 22 inches, are trimmed down with a chainsaw. Ellis found by trial and error that the perfect rotational speed for the blade is 700 rpm. Run it faster, and the blade wobbles and flexes.
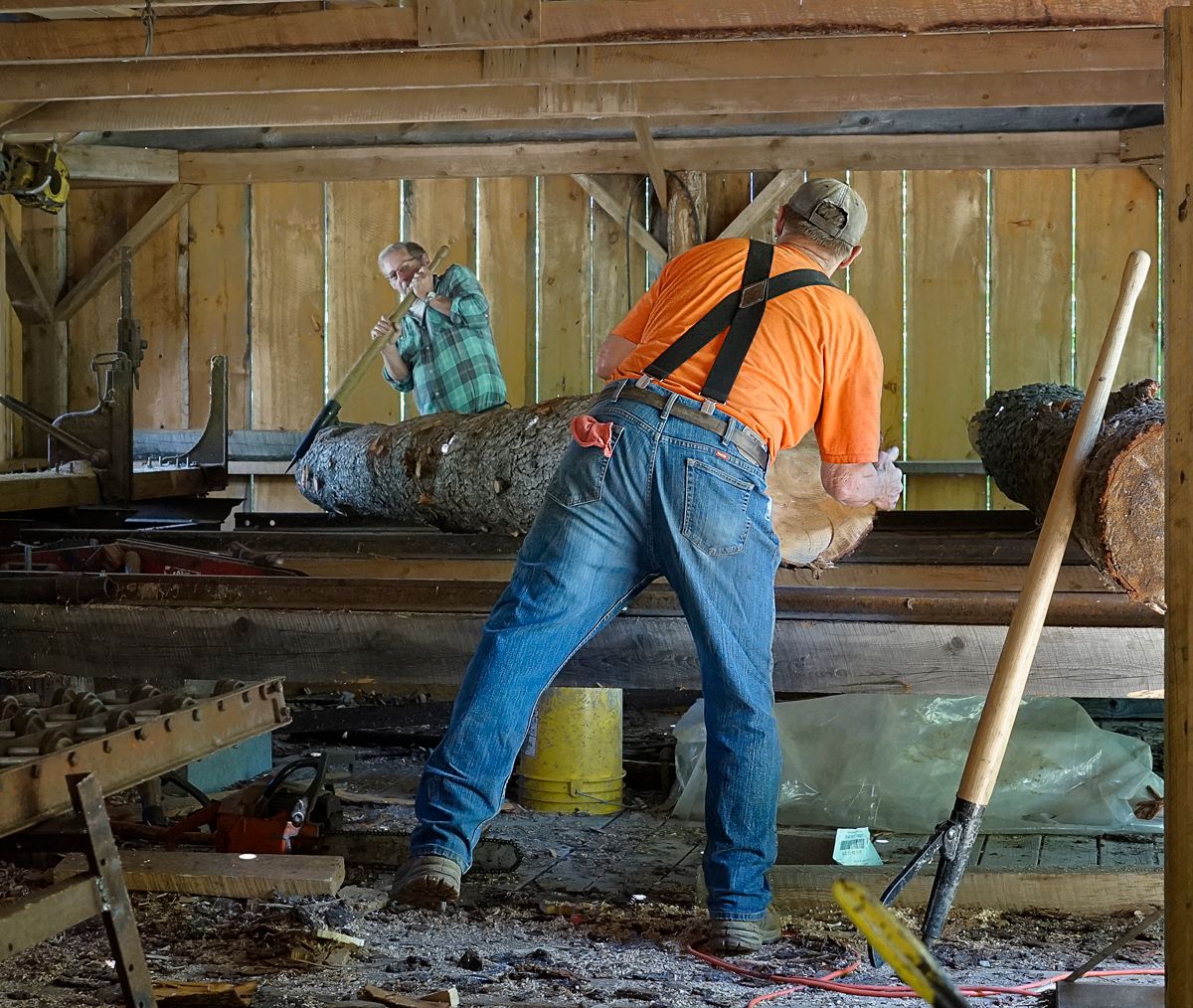
Ellis Paige and Pete LaPierre manuever a log towards the "carriage"on the left.
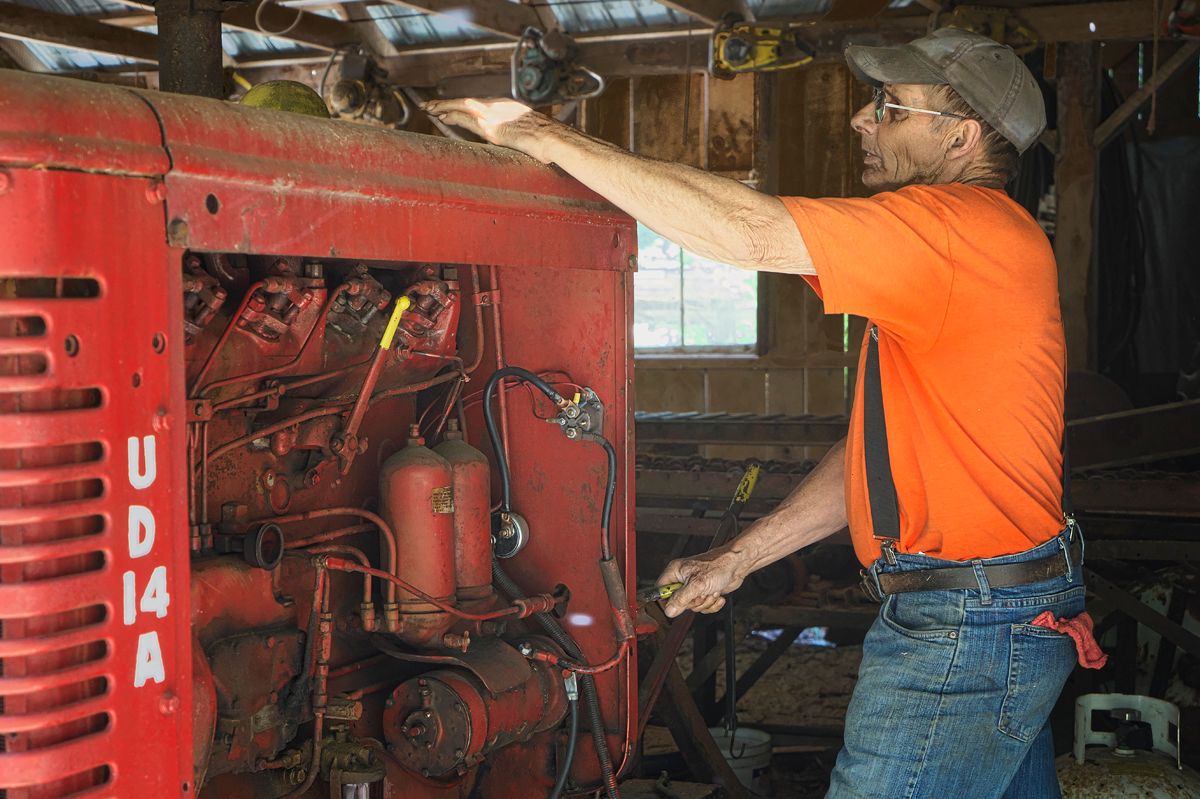
Ellis rigged up the motor of a 1945 International tractor to run the sawmill. The power take-off shaft of the tractor connects to the saw via a series of pulleys and belts that Ellis adapted from an old corn chopper. The pulleys reduce the motor speed of 1100 rpm to the blade rotational speed of 700 rpm.
The tractor engine itself is unusual in that it starts on gasoline, but once the engine has warmed up, it is manually switched to diesel. How the changeover from carburetor/gasoline to fuel injector/diesel was engineered remained a mystery until the engine burned out one of its "power cores." That forced Ellis to take it apart for a rebuild. His son-in-law searched the internet daily for a month before he managed to locate the replacement part.
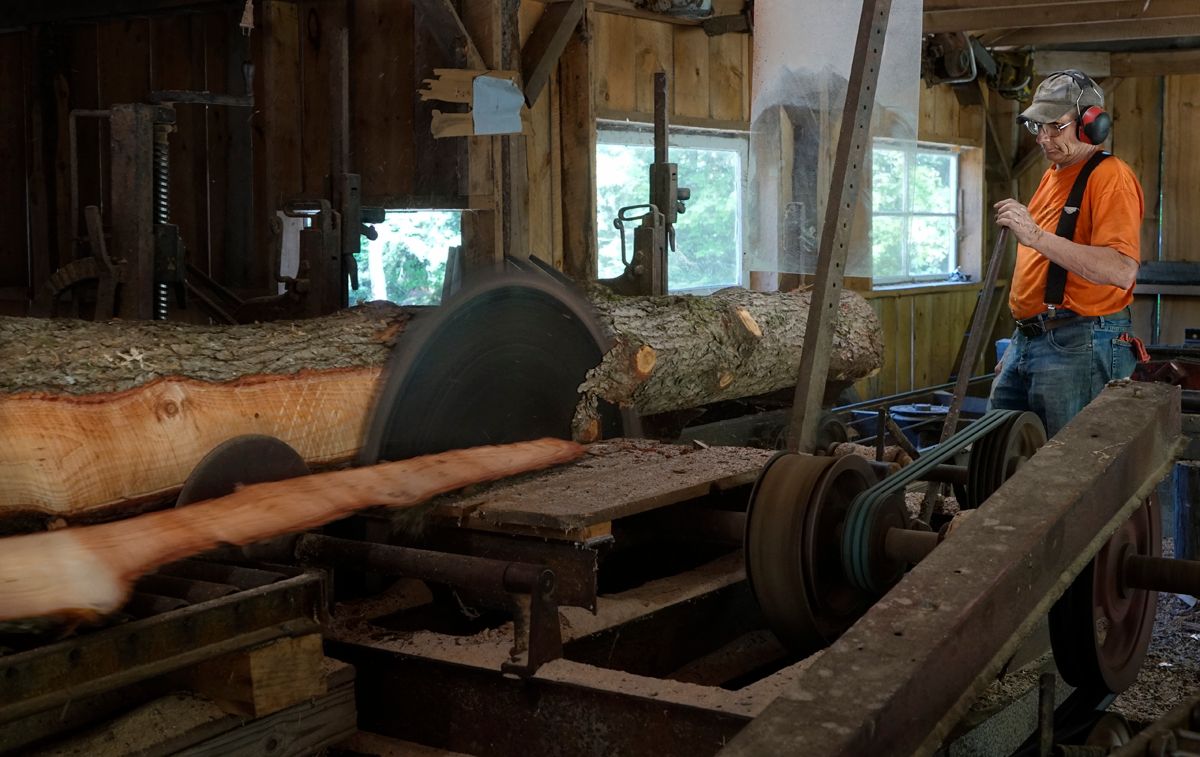
The log is secured on the carriage which glides forward on steel tracks and feeds the log through the saw at the pull of the lever. The lever also controls its return. The hanging piece of plexiglass shields Ellis from flying woodchips.
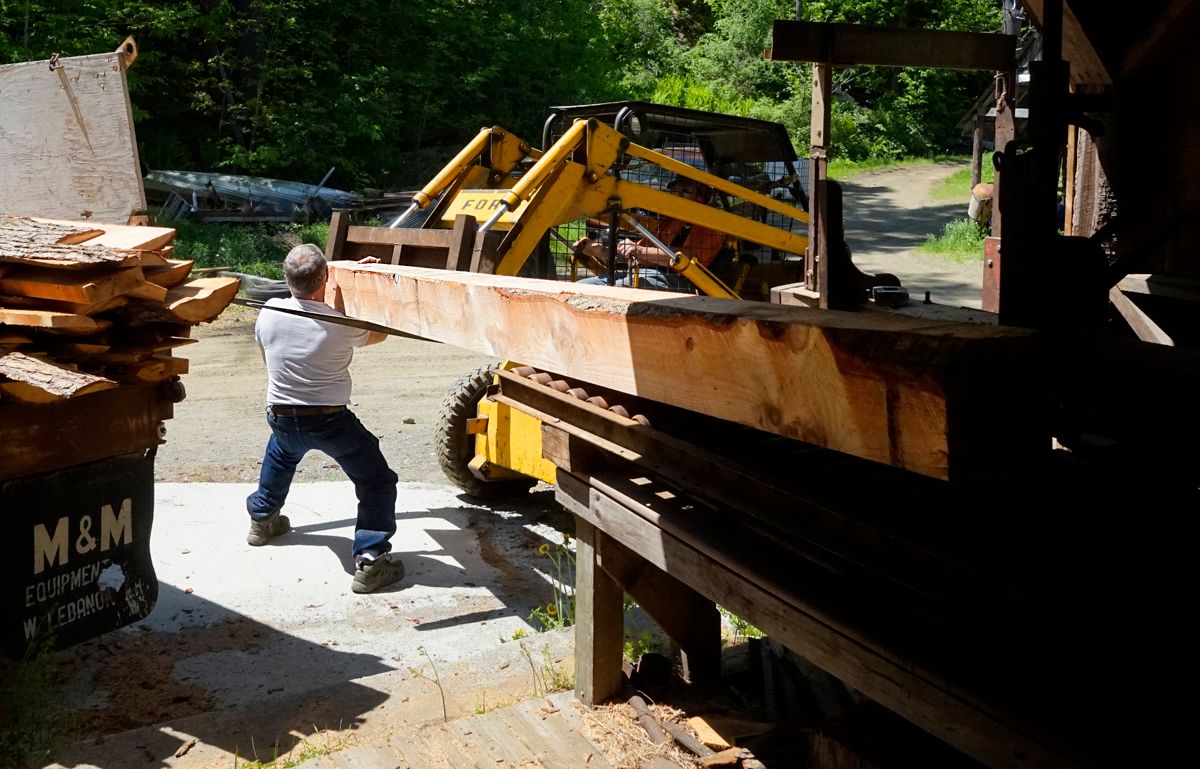
Pete loads a finished post onto the forklift.
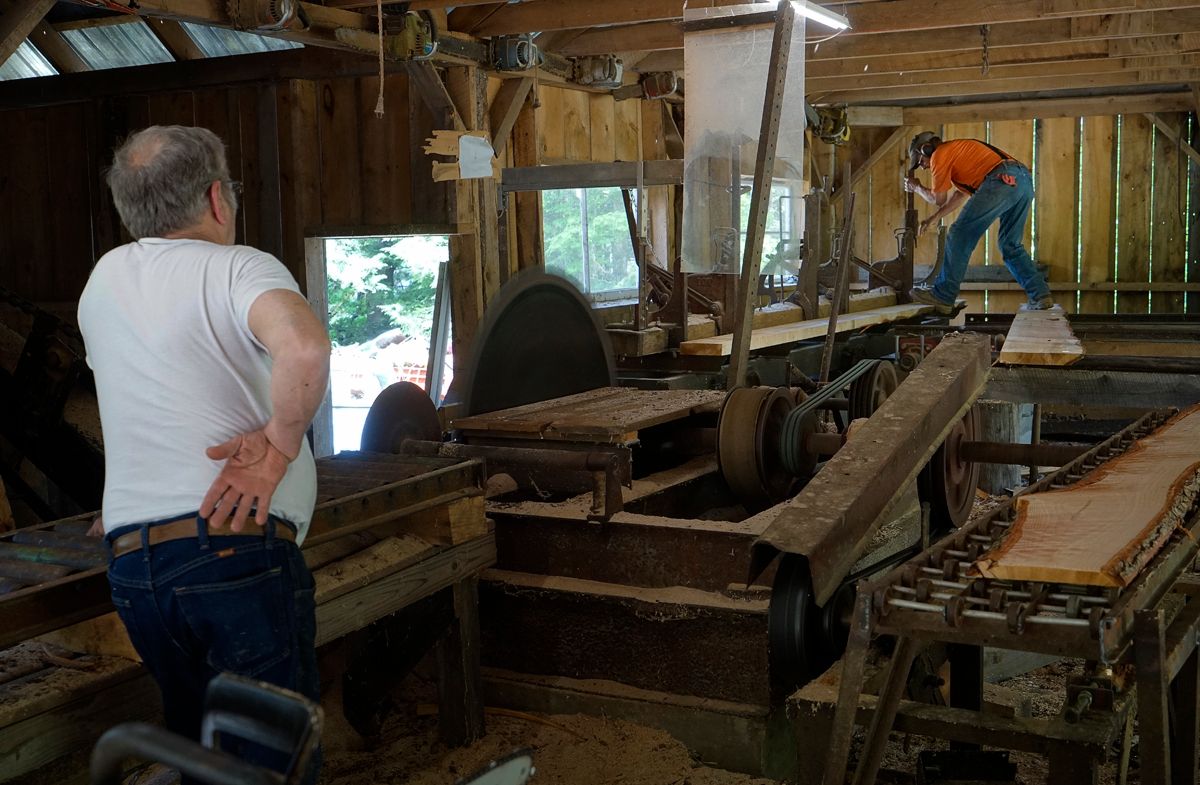
Ellis secures a partially sawn plank to the carriage.
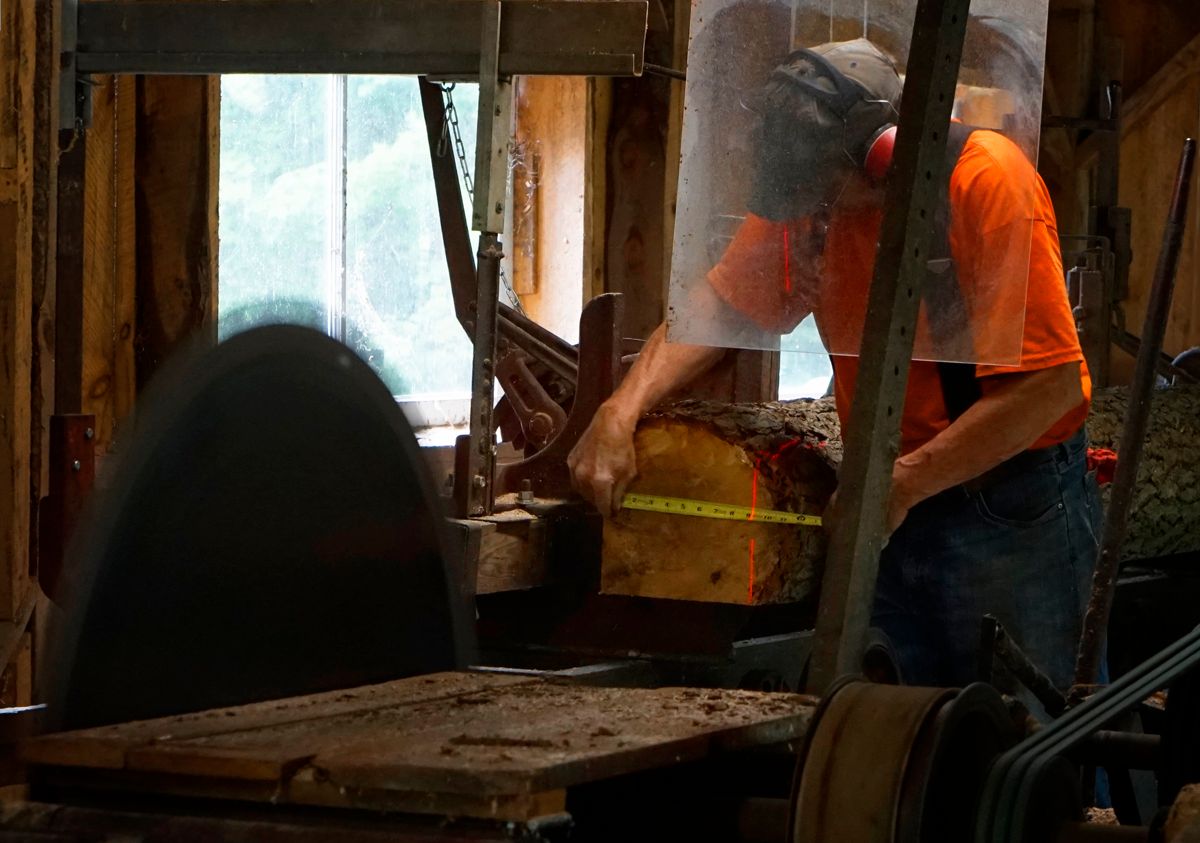
Dimensions are carefully set by moving the carriage sideways. The red line is the beam from a laser leveler that shows exactly where the saw blade will make the cut.
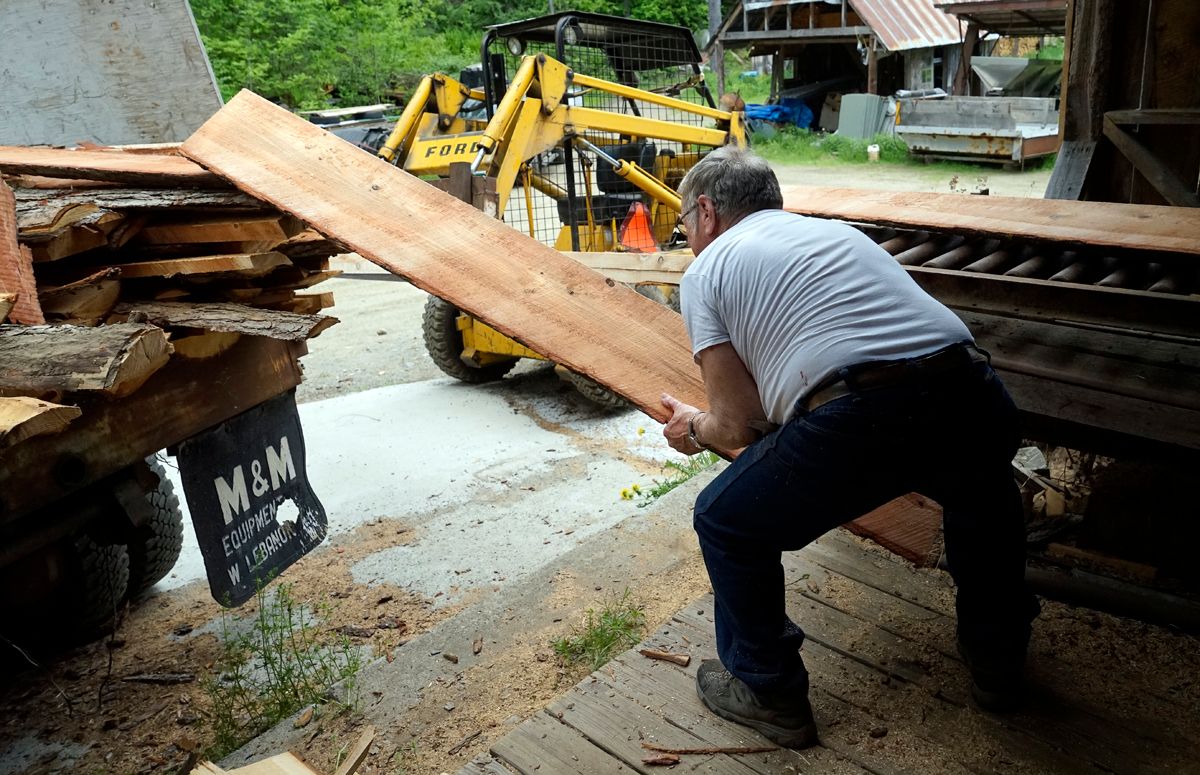
Slabwood cut from the outermost part of the log is set aside on the truck.
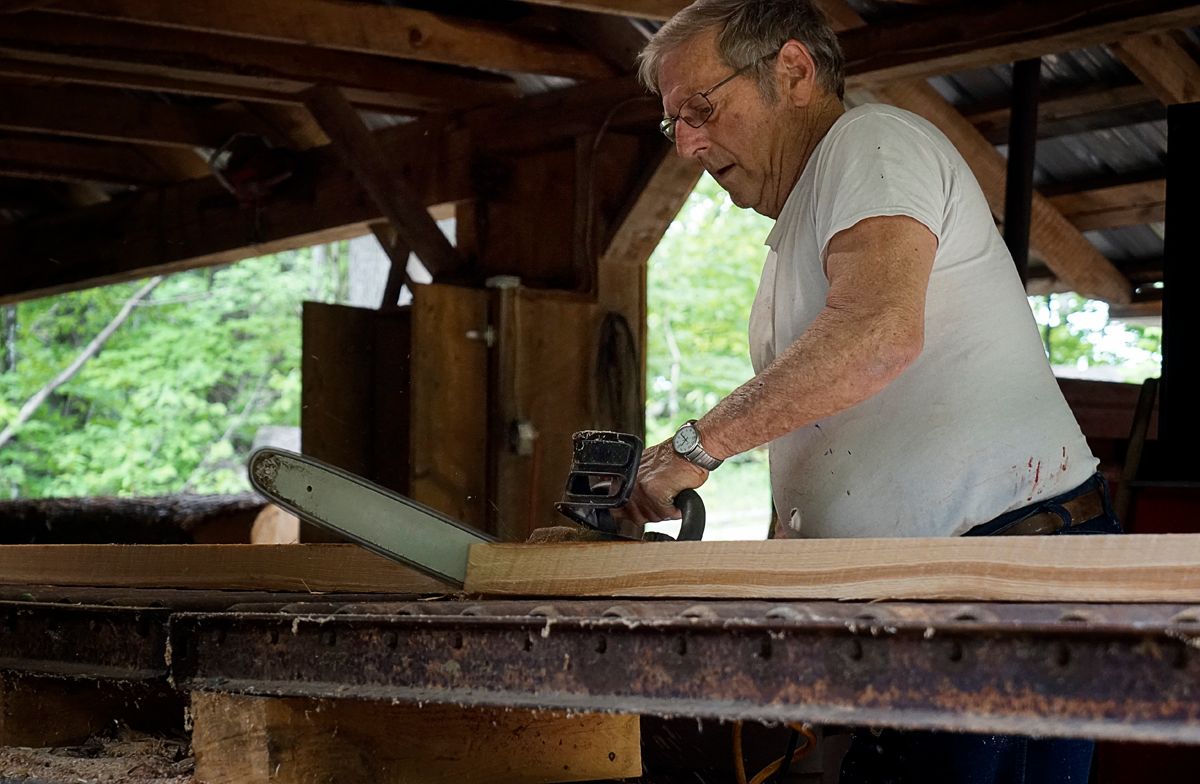
Pete saws planks to length.
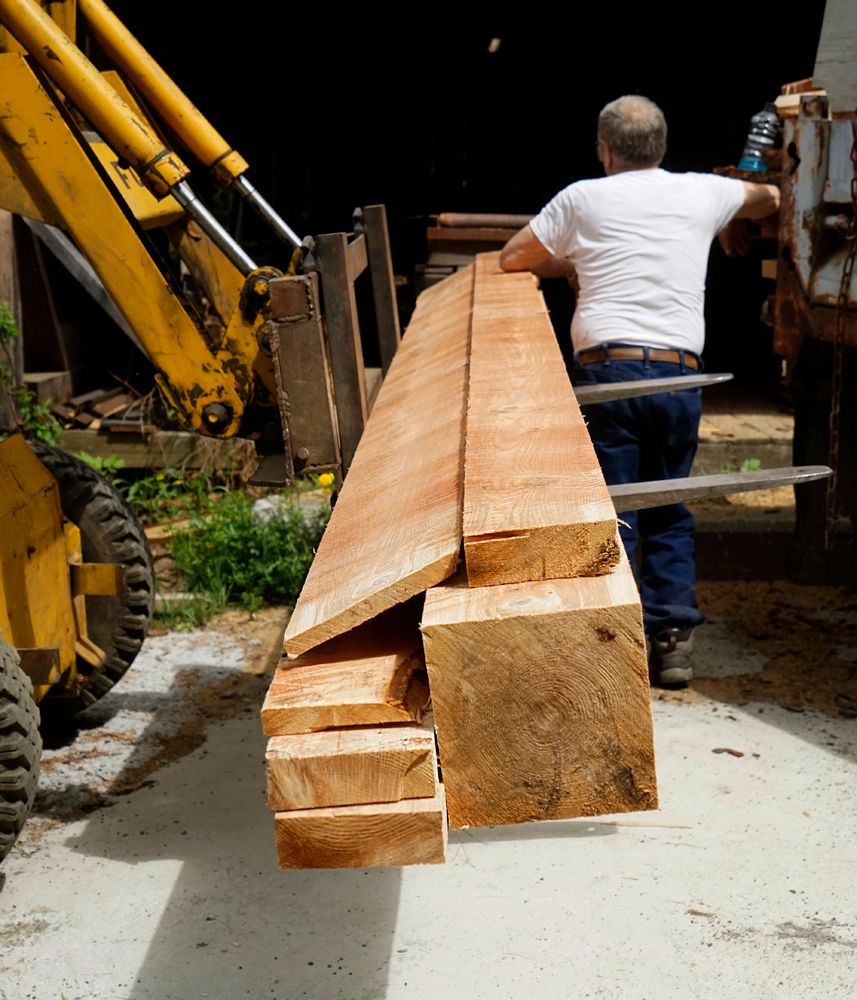
Lumber is stacked on the forklift.

The men communicate with hand signs. It's too noisy to hear anyone speak.
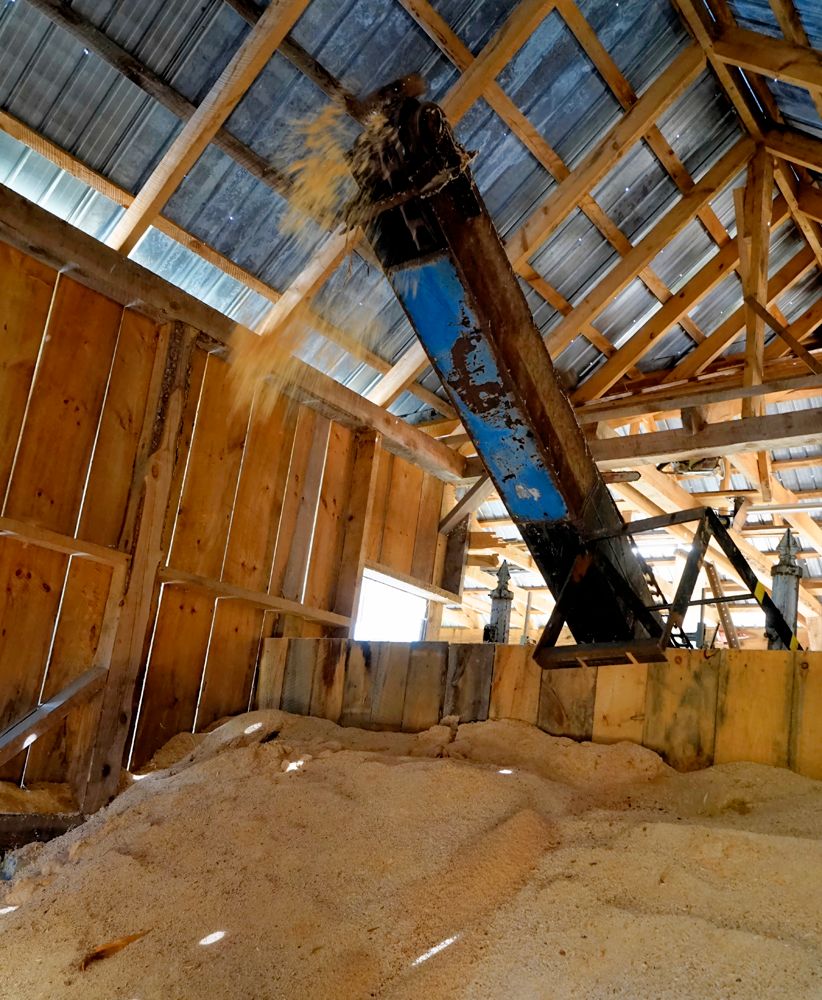
Sawdust is removed from beneath the blade by a conveyor chain of scoops that push the sawdust up an elevator and deposit it outside of the milling area. Ellis obtained the sawdust elevator from his neighbor, the late Gary Ulman, when Gary got out of the milling business. It was converted to run off the tractor motor using parts salvaged from old haying equipment. The elevator belt is moved by cog wheels that Ellis fabricated using sheet steel and a plasma cutter. While blowers are an option used by many sawmills to remove sawdust, Ellis points out that they jam whenever a knot of wood pops out of a board.
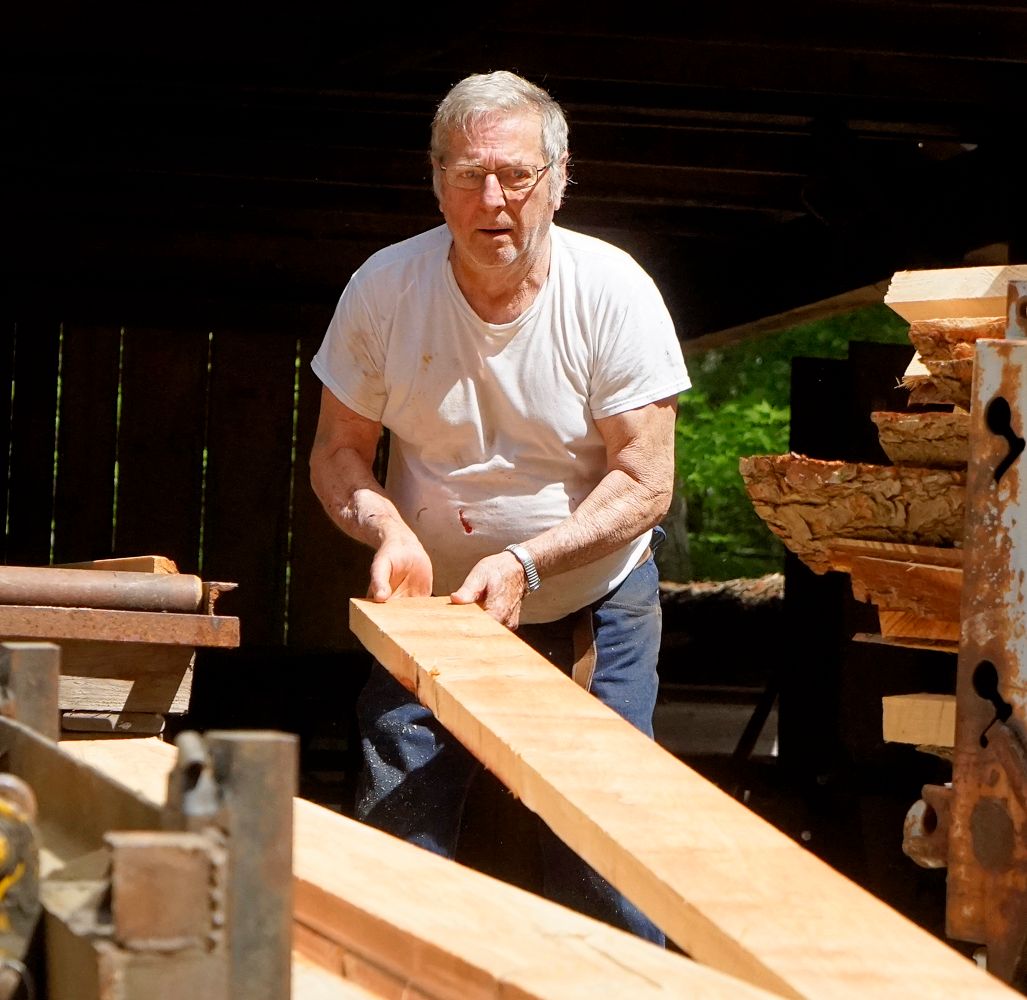
Pete carefully slides a board onto the pile on the forklift.
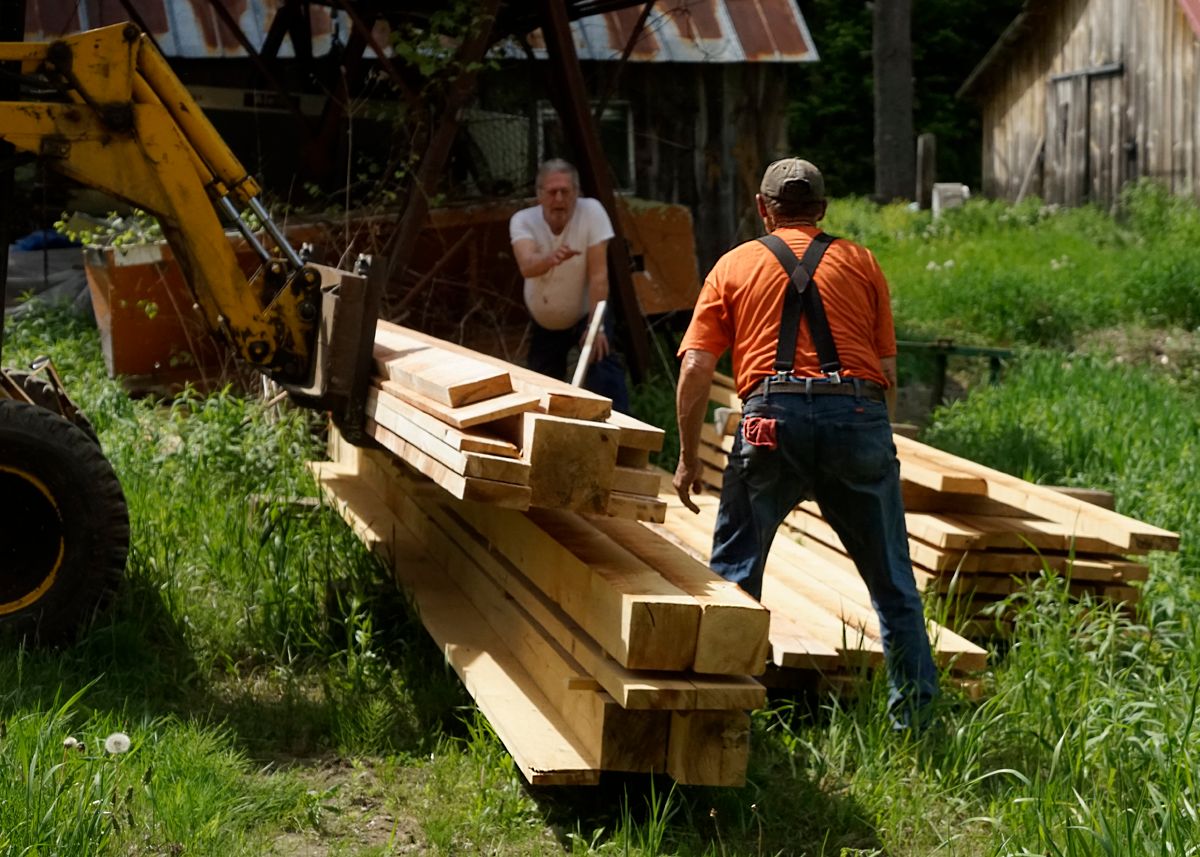
The final product. Ellis and Pete will carefully stack the cut lumber with "stickers" in between the layers to promote even drying. Some of the wood will be used to build a post and beam porch for Pete, and several posts will contribute to the reconstruction of an antique blacksmith's shop on Rt 113 in Thetford.
Though small sawmills are few and far between these days, there are still a couple more in our area, one on Route 25A on the east side of Mount Cube and one between Royalton and Randolph.